The principal activity of our company consists on trading new and used textile machinery, spare parts, and offering annexes services.
Our main aim is to establish a mutual and fruitful business relationship with our customers.
Our experienced and reliable staffs are willing to dedicate their time, effort and know-how to consulting, appraising and planning various stages of your textile business.

Indigo slasher yarn dyeing range with accessories direct warping & colour kitchen
- RAMMULIAN direct warping year 1990 working width 1500 mm model BMS-1400-E, can warp different widths of warp beams between 1400 mm and 2100 mm, flanges up to 1400 mm diam. HACOBA creel h type 195.585 with 672 spacing spindles, 230 mm. including 12 warp beams indigo slasher yarn dyeing range & colour kitchen
- MASTER indigo dyeing, working width 1800 mm, year 1996 / 2003, complete with KARL MAYER rotol sizing year 2005 RAMALLUMIN drying year 2005, rotol warping year 2003 entry from one beam creel for 12 beams, diameter 1250 mm width 1500 mm first tank nitrogen impregnation 36 meters yarn content year 2010 with 2 bowl padder 10 tons pressure, width 1800mm one soda treatment tank or pre-dyeing or washing, with 2 bowl padder 10 tons pressure, width 1800mm one reaction skying / oxidation section one steaming unit with 38 meter yarn content one pre-washing / dyeing unit, with padder 10 tons, width 1800 mm one reaction skying / oxidation section one pre-drying unit, 6 cylinders, diameter 640 mm, width 1800 mm six dyeing / washing units, each with 1 padder 10 tons, width 1800 mm each with one reaction skying / oxidation section one recycling unit heated dyeing bath + hydrosulphit dosing last two tanks with intensive washing chambers with 1 padder 10 tons, width 1800 mm ENDRESS & HAUSER ph control 3 units year 2007. pneumatic accumulator, maximum 135 mt capacity
- KARL MAYER rotol sizing year 2005 ww 2000mm one side loading creel for 6 beams, one RAMALLUMIN pre-dryer, 8 steam drying cylinders, diameter 800 mm, width 2000 mm year 2005, one KARL MAYER rotal double squeeze size box, 3 tons pressure, with 2 dip and 2 squeeze rollers, year 2005, humidity control system by RAMALLUMIN. year 2005, one RAMALLUMIN dryer, with 12 cylinders, diameter 800 mm, width 2000 mm one separating unit one rotal direct warping beamer, flange diameter 1250 mm, head stock working width 2500 dinax plc control
- LAWER MASTER colour kitchen year 1996 1 size kitchen consisting of 2 x preparation tanks 800 litre, 1 size cooker, 1 storage tank, 1 dye kitchen: 1 preparation tank, 2 dye stuff tanks, 2 feeding tanks, 2 dosing pumps, ss tanks 1 x 1000 litre 2 x 2000 litre 6 x 5000 litre tanks all with mixing units. LAWER PATERNOSTER dye store and weigh station
Specifications
ManufacturerMASTER
Year2003 Workin
...............................
02 JIGGER "KUSTER" type 268.17 - ww mm. 3200.
- year of1989 construction - currently installed and working.
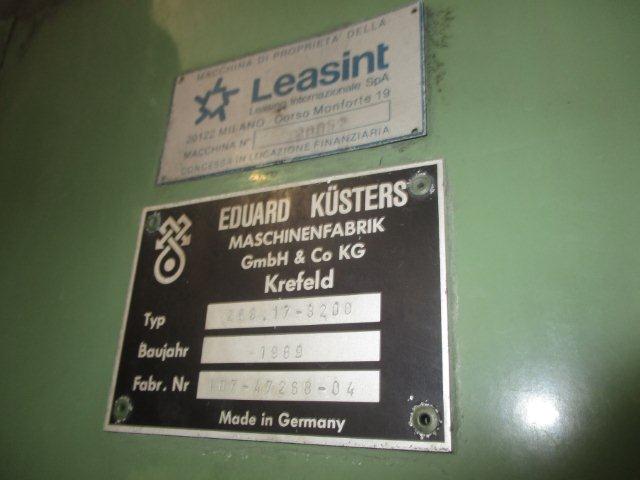
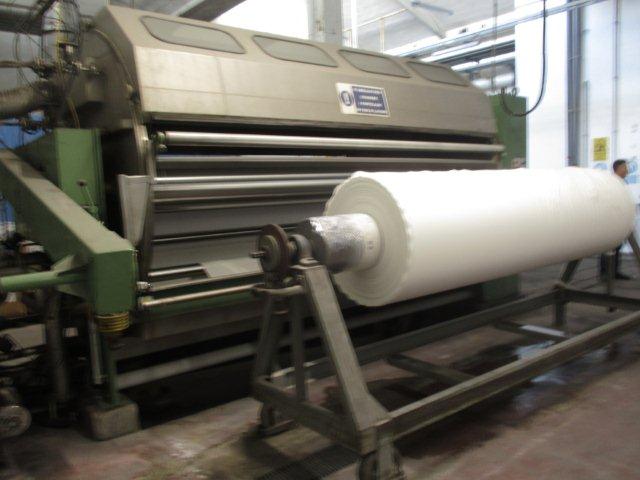
02 JIGGER "MEZZERA" mod. "VGM 1050" type MEDIUM
width mm. 2000.- work width mm. 1800.- with
rolls for a maximum of mm. 1050.-
Adjustable tension from 5 to 60 Kg. - (suitable for all types of Fabric)
"Direct" and "indirect" steam heating with thermoregulation.-
Heating with "indirect" coil at the hood with drip tray.
At the end of the dyeing cycle with "pendulum" device to avoid it imbalance for large weight rolls.
Automatic "zettatore" device for moving the fabric.-
Anti-crease bar device during the unloading of the fabric on G. R.
Hydraulic coupling device with a 1,3 / 8 "standard shaft with 6 grooves for the unloading fabric on the cart
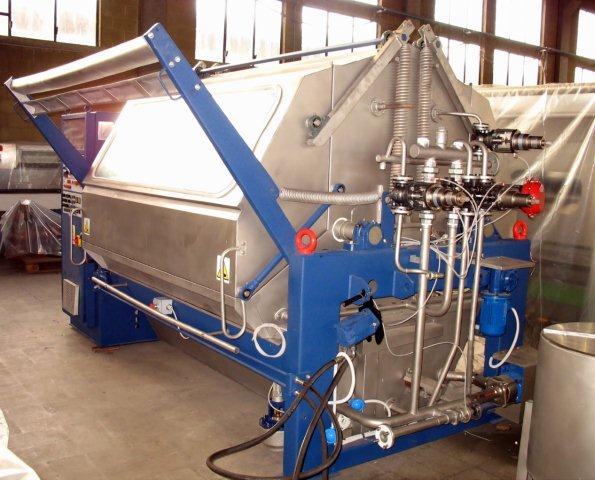
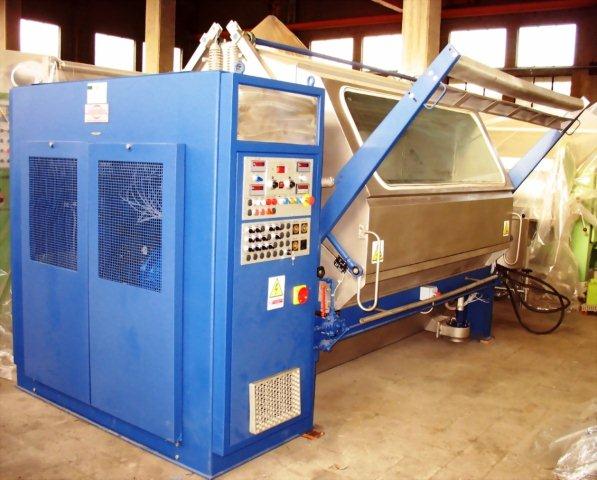
SPEROTTO-RIMAR-SANTEX GROP" SANFORT LINE type "FLEXA FSL 2000" suitable for woven / chain fabrics
- width mm. 2000.- useful width mm. 1850.
- consisting of: Input unit with motorized drive calender J-Box in stainless steel for fabric storage
- dancer cylinder for tension control and synchronization with the rest of the line
- "HERARD-LEIMER" type guide unit KF 20 " Humidifier unit comprising
- n ° 01 humidifier cylinder in stainless steel (perforated) with steam distribution system from inside to outside, covering special material to obtain a perfect steam distribution. Skew-against device (retort weaves suitable for Denim fabric) Horizontal hoist-equalizer lifter
- consisting of n ° 02 sections of 2.00 meters each - (for a total chain length of 4.00 meters) the first adjustable section with a conical field
- the second in the field parallel
- input with photocell probing groups Bank return unit (Rubber-belt) consisting of central cylinder "chrome-plated and mirror-polished with a diameter of mm. 610.- with rotary joint for steam heating and water cooling n ° 03 cylinders for retirement of the chrome-plated and mirror-polished rubber-belt-acvciaio with a diameter of mm. 210.- adjustment of the retirement cylinders by means of an activator controlled by a reduction motor - with automatic discharge of the tension every time the machine stops to avoid deformations on the rubber-belt with a water-cooling system - rubber-belt grinding device by means of a cylinder covered with abrasive paper - driven by a reductive motion - dust extraction Large-sized felt calender consisting of: control cylinder on a load cell for synchronization and control of the tension of the fabric between the rubber-belt group and the felt calender - cylinder diameter mm. 2000.-and diameter felt drying cylinder 800.- both cylinders are steam heated with rotary joints - automatic felt centering device - controlled by pneumatic pistons - device for checking the tension on the felt controlled by pneumatic pistons - control cylinder mounted on a charge cell for synchronization and tension control on the fabric between the felt calender and the cooling group.- Cooling unit consisting of n ° 03 steel cylinders with a diameter of mm. 650.- water cooler - complete with motor-reducers - the outlet consists of a stainless steel J-Box. For fabric accumulation - control cylinder mounted on load cell for synchronization and tension control on the fabric - between the cooling unit and the winding arm for Big roll and for the welder group.- Device for detecting the percentage of re-entry by means of encover (n ° 01 mounted on the cylinder inlet and the other mounted on the outgoing cylinder) Electric power panel containing: inverters for motors and PLC for the complete operation of the machine - control panel for adjusting working parameters - located on board the machine - with the possibility to control "strt - stop" emergency "increase - decrease" work ec. etc.
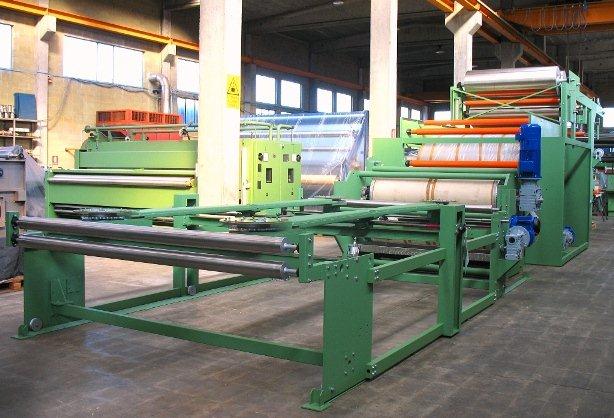
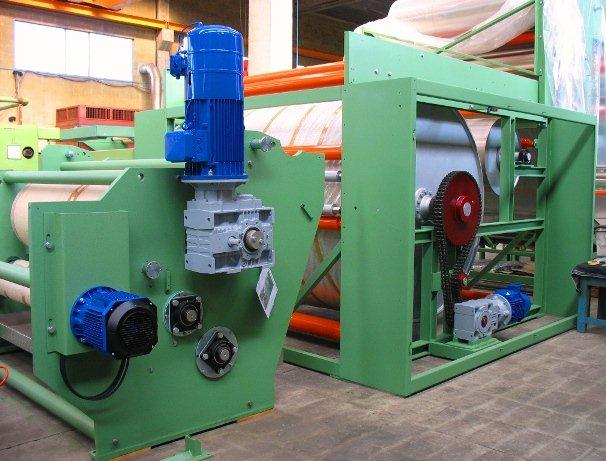